Contact information
- Qingdao Huasense Machinery Co., Ltd.
- Phone: 8613853201899
- E-mail: huaxin@huasense.com
- Fax: 400-86-00000
- skype: Fusce ac
Product Classification
Wechat Contact
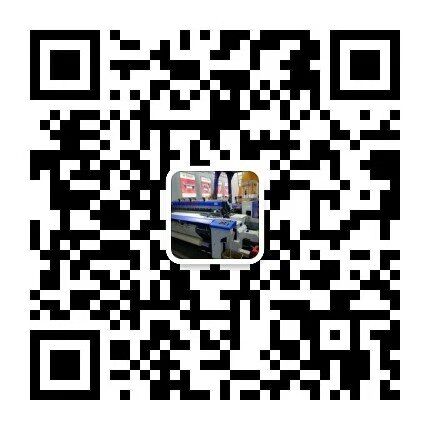
Feedback Message
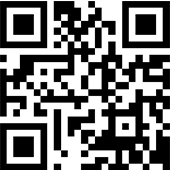
Shuttleless looms mainly include shuttle looms, water-jet looms, air-jet looms and rapier looms. Among them, the unit energy consumption of shuttle loom (calculated by weaving cloth per square metre) is low, followed by water-jet loom, and jet loom and rapier loom are high. Enterprises can not choose which kind of loom to buy only with the level of energy consumption as the main index, but textile machinery factories should pay attention to energy-saving technology when introducing new looms.
The energy consumption of air-jet looms is mainly due to the energy consumption of nozzles. The nozzle holes of auxiliary nozzles have been studied by various air-jet loom manufacturers for a long time. Single hole, porous, inverted cone holes and other shapes have been adopted. Many of them have been applied in practice. The auxiliary nozzles of various aperture shapes have their own advantages. Various innovations in nozzles (including main and auxiliary nozzles) and trachea can not only save energy but also improve weft insertion quality.
With the wide application of electronic technology in loom monitoring and monitoring, many enterprises have introduced new energy-saving technologies and new measures, such as the application of auxiliary nozzle solenoid valve in air-jet loom, which consists of four to six auxiliary nozzles equipped with one solenoid valve and two auxiliary nozzles equipped with one solenoid valve. The electronic control box controls the orderly switch of the solenoid valve. In order to achieve the purpose of airflow relay injection. It is reported that this new technology alone can save air consumption by 10%-15%. Taking a 190cm reed air-jet loom as an example, the weft insertion air consumption of one air-jet loom is 0.5-0.6 m3/min, 48 air-jet looms are equipped with air compressors of nearly 40 m3/min, and one 40 m3/min air compressor is equipped with a motor of several tens of kilowatts. Generally, there are 24-26 auxiliary nozzles in 190cm air-jet loom. The distance between each auxiliary nozzle in weft insertion channel is 70-80 mm. Because 4-6 auxiliary nozzles are equipped with one solenoid valve, that is, 4-6 auxiliary nozzles switch at the same time, it can not save gas consumption. At present, there are two auxiliary nozzles of air-jet loom equipped with a solenoid valve, only two auxiliary nozzles have the same switching time, which creates conditions for saving air consumption. With the increase of loom speed and the decrease of the number of auxiliary nozzles controlled by each solenoid valve, the speed of auxiliary nozzles is required to be accelerated. Without high-performance and high-speed solenoid valves, this technology can not be popularized.
In addition to the energy consumption of air weft insertion, the energy consumption of other mechanisms is also large, mainly the beating-up mechanism. There are two kinds of beating-up mechanism: crank-connecting rod mechanism and conjugate cam beating-up mechanism. Both mechanisms have their advantages and disadvantages. The comparison of production practice over the past 20 years shows that both beating-up mechanisms meet the production requirements. For individual heavy and wide fabrics, the conjugate cam beating-up mechanism has its outstanding advantages, while the crank-connecting rod beating-up mechanism is slightly deficient in this respect. For most products, the two organizations are identical. In terms of quantity, crank-connecting rod mechanism is the most widely used mechanism in air-jet looms. Rapier loom evolved from crank-connecting rod beating-up mechanism to conjugate wheel beating-up mechanism. The shuttle loom does not need the conjugate cam beating-up mechanism.
The second is the opening mechanism. Whether the cam openings or multi-arm openings are energy-intensive mechanisms. But the energy consumption of passive cam is slightly lower than that of active cam. Both cam openings have their own advantages and disadvantages. Users should choose and purchase them according to their specific conditions. Dobby openings consume more energy than cam openings. Toyota Corporation and Tsudaku Corporation of Japan have successively introduced an electronic dobby with a heddle and a servo motor, which eliminated electromagnets, cams and so on. The energy consumption is much lower than the existing electronic dobby, and the adjustment is also very convenient.
When it comes to air-jet looms, air compressors must be mentioned. At present, the air compressor used by domestic enterprises is not ideal, the efficiency of the compressor is low, and because of the large vibration and noise, the compressor should be installed at a certain distance from the air-jet loom workshop, so the energy loss of the pipeline is very large. Japan's air-jet loom factories use small-capacity air compressors. For example, 48 air-jet looms only need four small-capacity air compressors, three often open one standby, while the standby is not always shut down, but four equipment turn on in turn. It is installed not far from the loom, some even in the production workshop. From this point of view, energy consumption is definitely lower than ours.
Air compressor is divided into absolute oil-free and indirect oil-free through oil filtration. Oily air compressor is superior to absolute oil-free in operation efficiency, life and energy consumption. Twenty years ago, companies used absolutely oil-free air compressors. In recent years, many users have switched to air compressors with oil, and its price is much cheaper than that of absolutely oil-free air compressors. After continuous exploration and improvement, the air compressor with oil has first changed the variety of lubricating oil and used lubricating oil which can clean and remove oil stains. In case the filter screen fails and oil spills on the finished cloth, it can be eliminated in the process of post-processing, dyeing and finishing. The air compressor with oil also has its shortcomings. Its lubricating oil has a certain service life and should be replaced regularly. At the same time, the oil filter should be cleaned or replaced regularly.
In recent years, air compressor factories have also introduced electronic controlled variable frequency motor and continuously variable speed air compressor, which can save about 10% of energy. It can save energy because it can adjust the speed of the motor according to the amount of air consumption. Take 96 air-jet looms as an example, in general, the air supply is greater than the air consumption, because 96 looms always have several stops. Although one air storage cylinder can adjust the air volume, if the loom stops more, the air storage cylinder will stop when it is full of air compressor, and it will take 30 minutes for centrifugal air compressor to stop again. Turn on, no stopping or turning on. So they all take the way of non-stop venting, so some of the energy is wasted in vain. This energy-saving air compressor can solve the problem of emptying, thus saving energy.
Previous: 噴氣織機(jī)外發(fā)展趨勢(shì)
Next: 暫無